An OSHA emergency action plan template gives you a solid starting point for handling workplace crises, but a plan that actually works is so much more than a fill-in-the-blank document. It's a customized playbook that can turn potential chaos into a structured, life-saving response. Think of it as the script your team follows when the unexpected happens, ensuring everyone knows their role, from evacuation to first aid.
Why an EAP Is More Than Just a Compliance Document
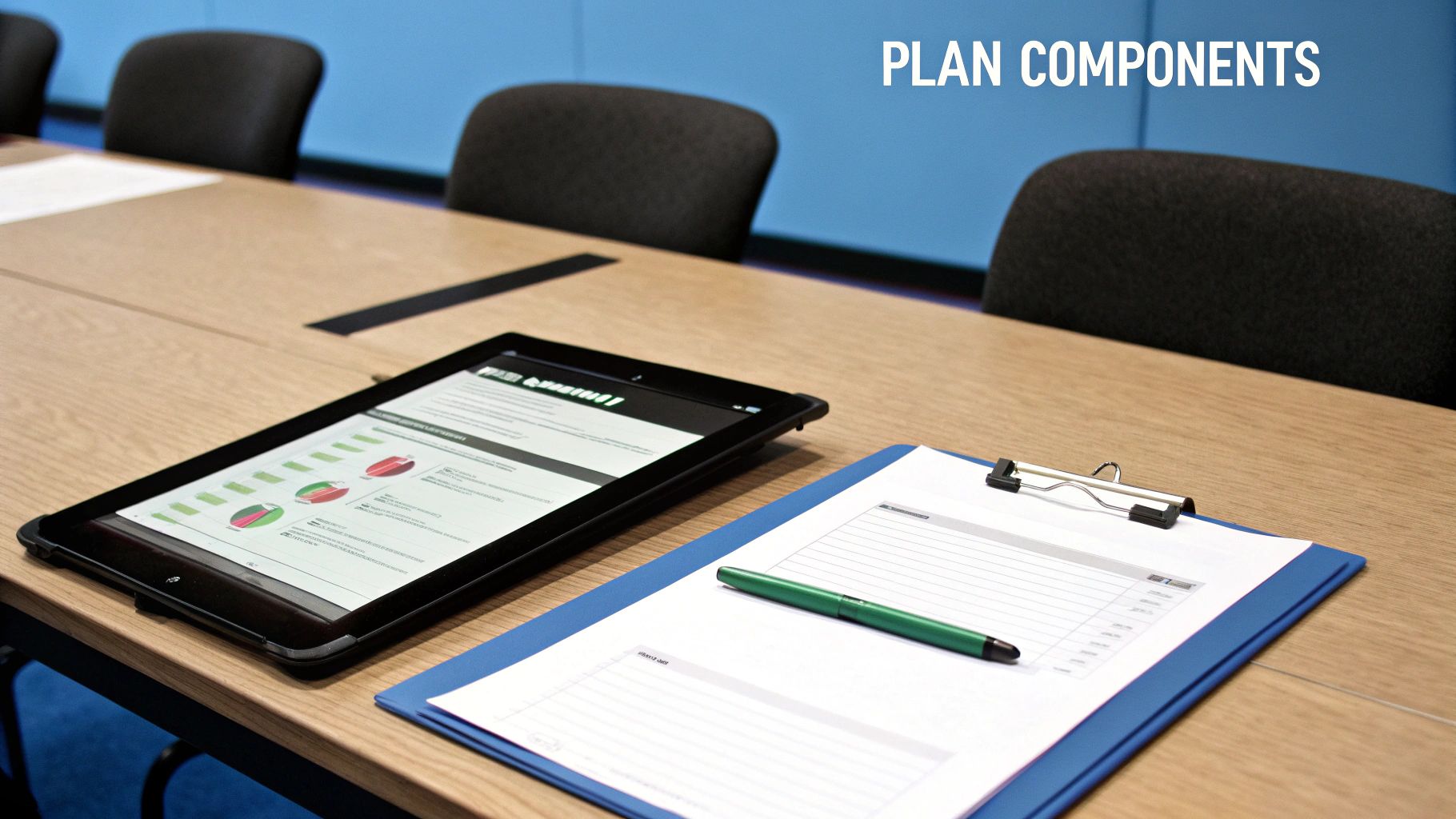
Let's be honest, when you hear "OSHA requirement," it's easy to think of it as just another box to check. But a well-crafted Emergency Action Plan (EAP) is one of the most vital documents for your business's survival and your team's safety. This isn't just about avoiding fines; it’s about protecting your people, your assets, and your ability to operate when a crisis strikes.
A clear plan replaces panic with decisive action. Whether the emergency is a fire, a sudden medical event, or a natural disaster, a documented and practiced strategy is the difference between a coordinated response and widespread confusion. It’s a living playbook for safety.
The Real Impact of OSHA and EAPs
The Occupational Safety and Health Administration (OSHA) was created for one reason: to ensure safe working conditions. Its regulations, including the one for EAPs, have had a massive, measurable effect. Since its inception in 1970, OSHA's oversight has contributed to a dramatic drop in workplace incidents.
Worker fatalities have fallen from about 38 per day in 1970 to around 15 per day in 2023. This significant improvement underscores the power of proactive safety planning.
These statistics aren't just numbers; they represent lives saved and injuries prevented. In FY 2024 alone, OSHA conducted 34,696 federal inspections to enforce safety regulations, including those for Emergency Action Plans. This consistent enforcement highlights the agency's commitment to workplace preparedness and its critical role in reducing risks. You can review the complete data and learn more about these safety findings on the official OSHA website.
Bridging the Gap Between Planning and Action
A great plan on paper is only the first step. The true value of an EAP is realized when your team has the skills and confidence to actually execute it. This is where hands-on training becomes indispensable.
Your EAP might outline procedures for medical emergencies, but what happens when an employee is exposed to a hazardous substance? This is a scenario where specific knowledge is crucial. Understanding how to respond safely is covered in specialized bloodborne pathogens training, which equips your team to handle contaminated materials without putting themselves or others at risk.
A functional EAP integrates seamlessly with practical skills training. It addresses a wide range of potential workplace incidents by preparing employees for scenarios such as:
- Sudden Cardiac Arrest: Guiding responders to AED locations and identifying trained personnel.
- Severe Bleeding: Outlining where bleeding control kits are stored and who is trained to use them.
- Chemical Spills: Specifying evacuation routes away from the hazard and procedures for decontamination.
- Fires: Clearly marking exits and assembly points and designating roles for floor wardens.
Ultimately, a robust EAP doesn't just satisfy a regulatory requirement. It builds a culture of safety, empowering your team with the knowledge and tools to act decisively and protect one another when it matters most.
Decoding the Core Components of a Compliant EAP
So, what does OSHA actually want to see in your Emergency Action Plan? It’s not just a vague suggestion to “be prepared.” The agency lays out specific, non-negotiable elements that are the absolute bedrock of any compliant EAP. I tell clients to think of these not as bureaucratic hurdles, but as the essential ingredients in a recipe that literally saves lives.
Each component serves a very clear purpose. For instance, having "procedures for reporting emergencies" isn't just about checking a box; it's about creating a lightning-fast alert system that shaves precious seconds off your response time. When someone knows exactly how to sound the alarm, help gets there that much sooner.
The Minimum Requirements for Your Plan
The Occupational Safety and Health Administration (OSHA) is crystal clear: employers who need an EAP must meet specific minimum requirements. According to the official regulation, OSHA standard 1910.38, the plan needs to detail everything from how to report a fire to how you'll account for every single employee after an evacuation. It’s a comprehensive look at your emergency response.
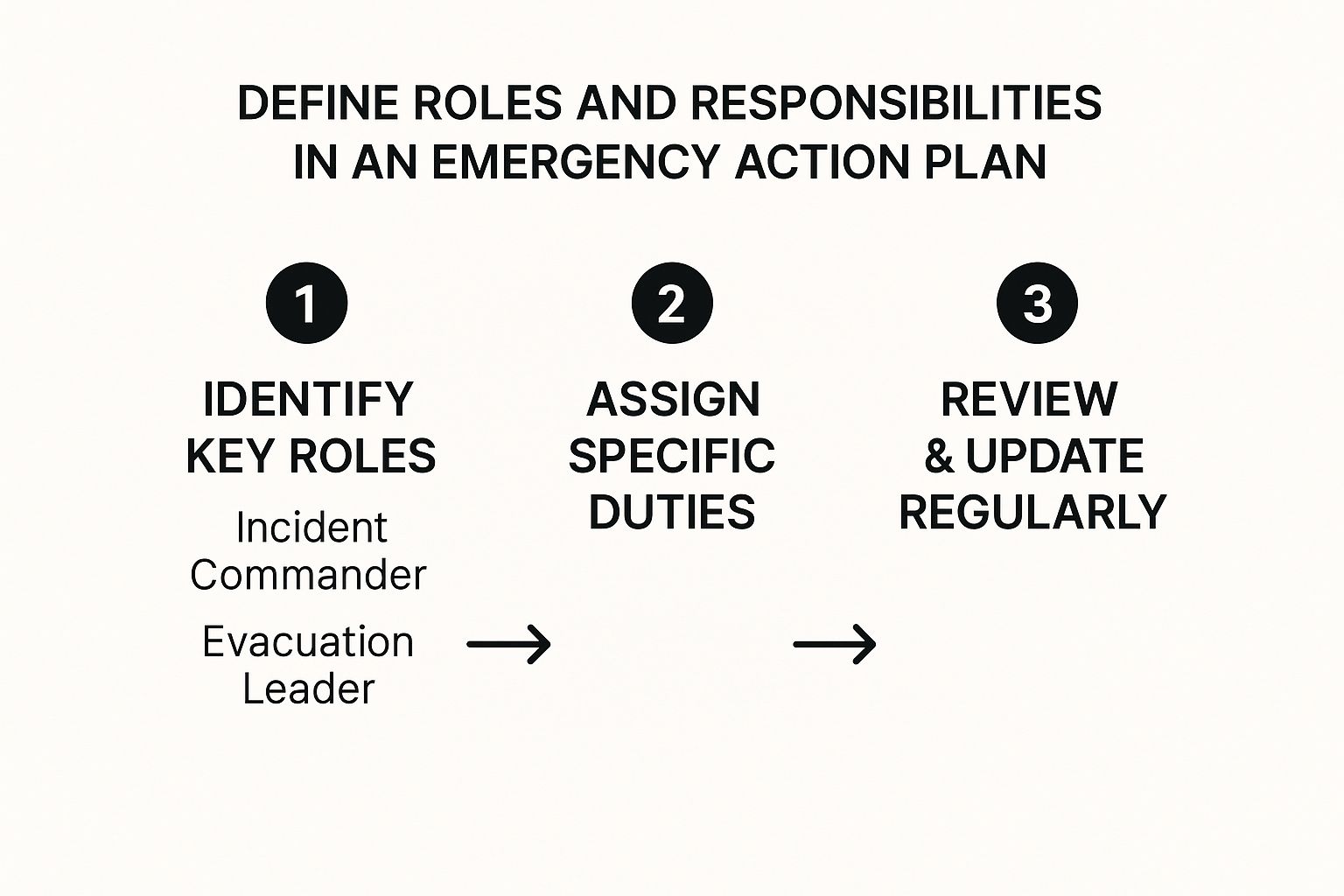
This guidance underscores a point I always emphasize: an EAP must be tailored to your specific worksite. It's not a one-size-fits-all document you can just download and forget. To really bring these rules to life, let's break down what they mean in the real world.
The table below translates OSHA's formal requirements into the practical, on-the-ground actions you need to plan for.
OSHA Emergency Action Plan Required Elements
Required ComponentWhat It Means in PracticeExampleEmergency Reporting ProceduresHow does an employee report a fire, medical crisis, or spill? You need a defined, primary method.Pulling a manual fire alarm, dialing a specific internal extension (e.g., x5555), or using a designated two-way radio channel.Evacuation Policy & ProceduresThis covers when to evacuate, the types of evacuations (e.g., shelter-in-place vs. full site), and the specific escape routes from every part of your facility.Clearly marked exit routes on posted floor plans, with primary and secondary paths identified for all work areas.Critical Operations ShutdownWho stays behind (briefly) to shut down machinery, turn off gas lines, or secure sensitive data? These employees need unique instructions.A designated maintenance worker is trained to shut down the main HVAC system before they evacuate, preventing smoke from circulating.Employee AccountabilityHow will you know everyone got out safely? This requires a clear procedure and a designated meeting spot.A headcount at a pre-determined assembly point in the north parking lot, conducted by department supervisors.Rescue & Medical DutiesIf you have an in-house response team, their specific roles and training must be clearly defined.Naming the certified first-aid responders on each shift and listing the location of AEDs and trauma kits.Key ContactsWho can employees contact for more information or an explanation of their duties under the plan?Listing the names and job titles of the facility's Safety Coordinator and all department heads responsible for the plan.
Each of these elements plays a vital role. Without a solid accountability procedure, for instance, you could have chaos at your assembly point, making it impossible to know if someone is still inside.
Defining Roles and Responsibilities
A plan without assigned roles is just a piece of paper. You absolutely have to designate and train a team to lead the charge during an emergency. This creates a clear chain of command and prevents that dangerous hesitation when every second counts.
Think of it this way: when the fire alarm goes off, people will look for a leader. Your plan must tell them who that is.
An effective EAP clearly identifies who is in charge. This could be an Emergency Coordinator or an Incident Commander who has the authority to make critical decisions, such as ordering an evacuation.
Rescue and Medical Duties
Does your plan call for certain employees to perform rescue or medical tasks? This is a huge responsibility and requires special attention in your EAP. You can't just ask for volunteers when an incident happens.
If you have an in-house team, OSHA requires you to ensure they are:
- Properly Trained: They need certified training in first aid, CPR, and any other relevant skills for your workplace hazards.
- Properly Equipped: They must have immediate access to first aid kits, AEDs, and any necessary personal protective equipment (PPE).
- Clearly Identified: Everyone in the workplace should know who these designated responders are, perhaps by a specific color vest or ID badge.
It's crucial to document their roles, their training records, and the procedures they should follow. Seeing how other organizations handle this can be incredibly helpful. For a closer look, check out these real-world emergency action plan examples to see how different businesses structure these critical roles.
Finally, the plan must list the names or job titles of people who can provide more information. This simple step ensures any employee, at any time, can get clarification on their role or the plan itself. It promotes transparency and keeps the EAP a living, useful document for everyone it's designed to protect.
How to Customize Your EAP Template for Your Workplace
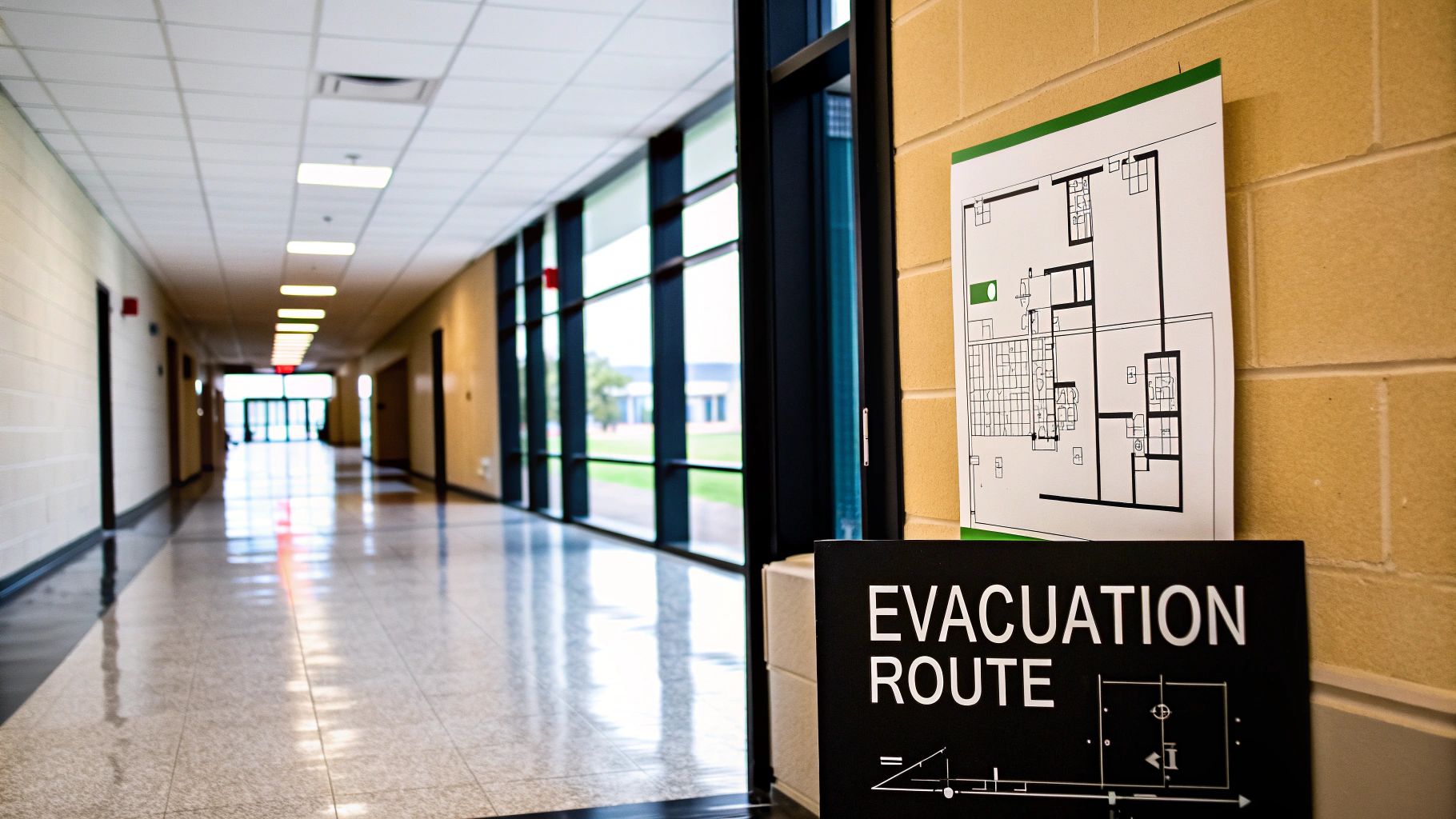
Grabbing an OSHA emergency action plan template is a fantastic first step. But think of it like a blueprint for a house—it gives you the general layout, but it doesn't account for the unique plot of land you're building on. Your workplace has its own terrain, and this is where customization turns a generic document into a functional, life-saving tool.
A template is the starting line, not the finish line. The real work starts when you begin asking site-specific questions and tailoring the content to the realities of your daily operations. That’s how you build a plan your team can actually use when the pressure is on.
Conduct a Site-Specific Hazard Assessment
Your first job is to walk through your entire workplace with a critical eye. You're hunting for every potential emergency scenario, from the common stuff to the truly location-specific. A manufacturing plant in Kansas faces a very different set of environmental risks than a dental office in coastal Florida.
To get started, ask yourself these questions:
- Environmental Risks: Are you in an area prone to tornadoes, hurricanes, earthquakes, or floods?
- Workplace-Specific Hazards: Do you handle hazardous chemicals, operate heavy machinery, or store combustible materials?
- Human-Caused Events: What's the plan for medical emergencies, active aggressor situations, or fires?
- Utility Failures: How would you manage a prolonged power outage or a sudden loss of water?
By identifying your specific vulnerabilities, you can move beyond a generic fire drill and build procedures for the situations your team is most likely to face. This focused approach is the core of effective emergency planning.
OSHA's entire philosophy around EAPs is that they should be living documents, constantly evolving based on what you learn from these risk assessments. It's about creating a true culture of readiness, not just checking a box.
Answering the Critical Questions for Your Plan
Once you know your risks, you can start plugging the details into your EAP template. The answers to these questions will form the heart of your customized plan, transforming it from a simple checklist into an actionable guide.
Personnel and Layout Questions:
- Assembly Points: Where is our primary assembly point? Is it a safe distance from the building? What about our backup location if the primary one is blocked or unsafe?
- Chain of Command: Who is our designated emergency coordinator? Crucially, who are the backups if that person is out sick, on vacation, or among the first impacted?
- Floor Wardens: Who is responsible for sweeping each area or floor to confirm everyone has evacuated?
- Assistance for Others: How will we assist employees or visitors who have mobility challenges or other disabilities? Who is specifically assigned to help them?
Remember, the goal is to leave no room for guesswork. In a real emergency, people don't have time to figure things out. Your plan must provide clear, direct answers.
As you adapt your EAP, keeping track of changes is essential. You need to make sure everyone always has the latest version. A plan is only effective if everyone is working from the same page, and learning about document version control best practices can help you manage updates without causing confusion.
Mapping It All Out
Don't just write down your evacuation routes—show them. One of the most powerful ways to customize your EAP is to include detailed, easy-to-read floor plans.
Your maps should clearly mark:
- Primary and secondary exit routes from every single area.
- The locations of fire extinguishers, fire alarm pull stations, and AEDs.
- The designated outdoor assembly points.
- The location of first-aid kits and other emergency supplies.
Post these maps everywhere—in break rooms, in hallways, and near every exit. When an emergency hits, a clear visual guide is much easier for a panicked mind to process than a page of text. It makes the plan tangible and accessible for every single employee, regardless of their role.
Training Your Team to Put the Plan into Action
Let's be honest. A brilliant, perfectly customized OSHA emergency action plan template is completely useless if it just lives in a binder on a dusty shelf. Its real value isn't in its existence; it's in its execution. This is where the most critical part begins: putting that plan into motion through effective, ongoing training.
Simply emailing the EAP to your staff and hoping they read it isn't training. Not even close. True preparedness comes from repetition and hands-on practice, turning theoretical knowledge into an instinctive reaction. When an alarm sounds, you don’t want your team trying to remember what a document said. You want them moving on muscle memory.
Moving Beyond the Annual Meeting
The old model of a once-a-year safety meeting is outdated and, frankly, ineffective. For an EAP to really stick, it needs to be an ongoing conversation, not a one-time lecture. This means weaving it into the very fabric of your company culture, right from an employee's first day.
New hire onboarding is the perfect time to start. Introduce your EAP alongside other day-one essentials. Don't just hand them a paper; walk new employees through the evacuation routes, show them the assembly points, and point out exactly where the fire extinguishers and first-aid kits are. This sets the tone from the get-go that safety is a shared responsibility.
Drills That Build Real Skills
Regular drills are non-negotiable, but their effectiveness hangs entirely on how you run them. A predictable fire drill where everyone casually strolls out to the same spot in the parking lot might check a box, but it doesn't build real-world resilience.
To make your drills meaningful, you need to mix it up:
- Vary the Scenarios: Don't just practice for fires. Run drills for medical emergencies, sheltering in place for severe weather, or even chemical spills if that's a risk at your facility.
- Block an Exit: In a real crisis, a primary exit might be blocked by fire or debris. During your next drill, tape off a main exit route. This forces your team to think on their feet and use their secondary path, testing their actual problem-solving skills under pressure.
- Practice Accountability: Go through the entire motion of your accountability procedure. Have your designated floor wardens or supervisors conduct a full headcount at the assembly point. This is how you find out if your process is smooth or clunky before it counts.
After every single drill, hold a quick debrief. What went well? Where was there confusion? Use that immediate feedback to tweak your plan and patch up any weak spots.
Specialized Training for Key Personnel
While every employee needs to know the basics, your emergency coordinators and response team members require a higher level of training. These are the people everyone will look to during a crisis. They have to be equipped with specialized knowledge and the authority to act.
Their training needs to go beyond the basics, covering decision-making under pressure, clear communication protocols, and how to coordinate with outside first responders. They are the calm in the storm, and that confidence only comes from advanced preparation.
This is also where professional, hands-on certification becomes essential. Your EAP might say that designated personnel will provide medical aid, but that’s only possible if they have the skills. Equipping your team with CPR, AED, and First Aid certifications gives them the tangible ability to save a life. You can check out our guide on tips for implementing and maintaining effective CPR training programs in the workplace to see how a structured approach can build a team of confident responders. This is the training that bridges the gap between the plan on paper and the life-saving actions needed in a real emergency, making your workplace genuinely safer.
Common EAP Mistakes and How to Avoid Them
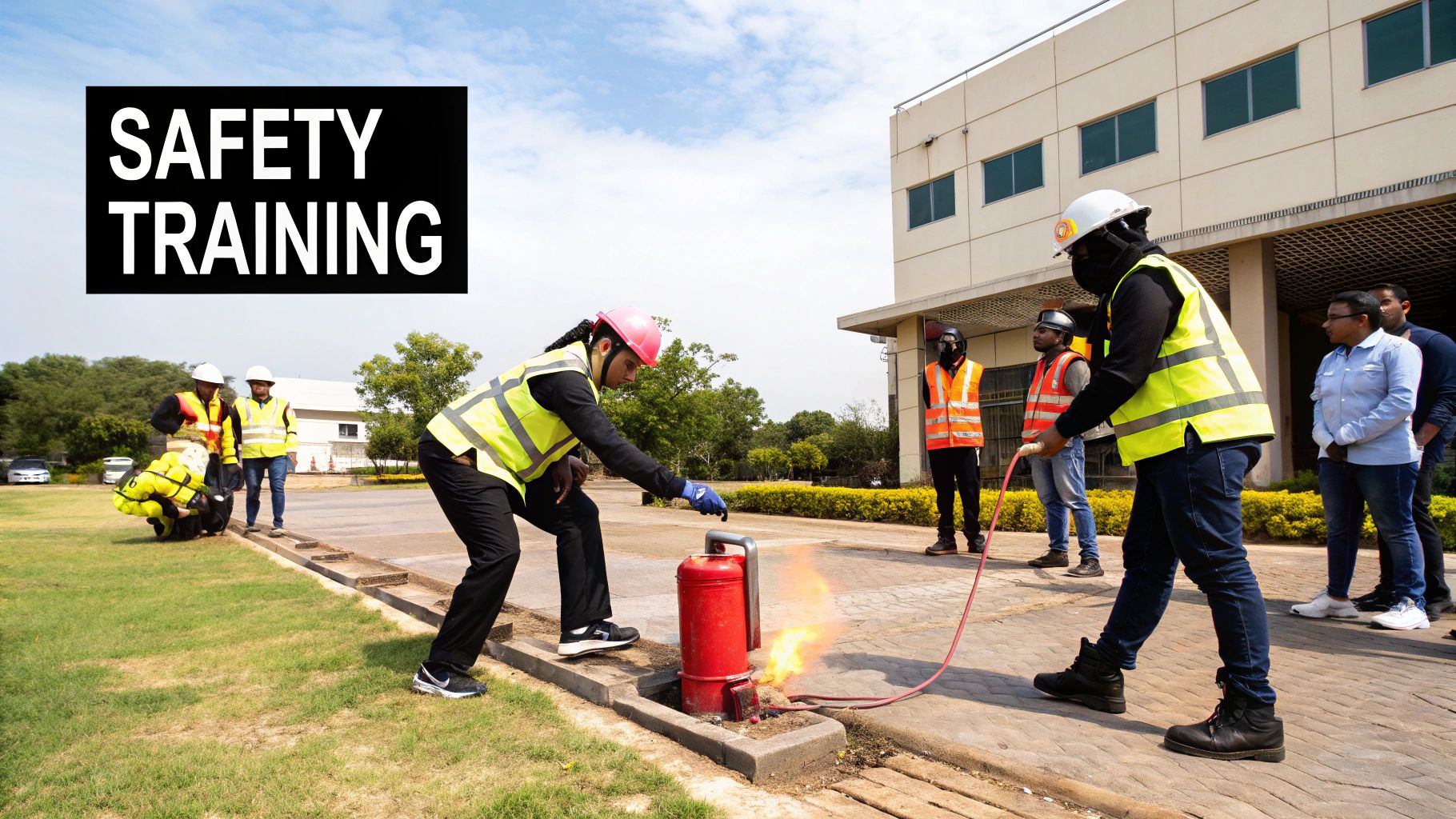
Learning from where others have gone wrong is one of the smartest ways to strengthen your own safety strategy. I've seen it time and time again—even with the best intentions and a solid OSHA emergency action plan template, businesses often stumble into predictable pitfalls. These common errors can unfortunately render a plan useless in a real crisis.
Think of this as a quick-reference audit for your own EAP. By recognizing these mistakes, you can find and fix dangerous gaps before an emergency strikes. Your plan needs to be a reliable, clear-headed guide, not a source of confusion when every second counts.
The "Set It and Forget It" Mindset
This is easily the most common—and most dangerous—mistake I see. A business puts in the work to create an EAP, files it away in a binder, and ticks a box. Job done, right? Not quite.
Workplaces are living, breathing environments. A plan that was perfect a year ago might be dangerously outdated today. This "set it and forget it" approach leads to plans with wrong contact numbers, obsolete evacuation routes, and names of employees who left months ago.
The core problem is treating the EAP as a static document instead of a living one. Your emergency plan must evolve right along with your business to have any chance of being effective.
To fix this, get a mandatory EAP review on the calendar at least once a year. You should also review it anytime there's a significant operational change. This proactive habit ensures your plan always reflects the reality of your workplace.
Overlooking Personnel Changes
Your plan depends on people, and when those people change, the plan can fall apart. A massive oversight is failing to update the EAP when key personnel—like an emergency coordinator or floor warden—leave the company.
Imagine an evacuation where everyone is looking for guidance from a supervisor who quit two months ago. The confusion that follows wastes precious time and can quickly escalate into panic.
Here’s how to get ahead of this:
- Make it part of HR. Integrate EAP updates directly into your employee offboarding process. When a key person resigns, their emergency duties must be immediately reassigned.
- Use job titles, not names. Designating "Shift Supervisor" or "Front Desk Manager" instead of "John Doe" makes the plan far more resilient to staff turnover.
- Cross-train your team. Have multiple people trained for critical roles. This creates built-in redundancy, so one person's absence doesn't cripple your entire response.
Using a Generic Template Without Customization
Downloading a generic template is a fantastic starting point, but that's all it is—a start. Too many businesses simply fill in their company name and call it a day. This creates a plan that's completely disconnected from the unique realities of their work environment.
A template won't know that your back exit leads to a fenced-in area or that you store flammable chemicals in the west wing. These site-specific details are what make a plan truly work. Just as there are common pitfalls in emergency planning, avoiding errors is crucial in other business operations. For example, you can learn about common mistakes in video conferencing to ensure your virtual meetings run smoothly.
Neglecting Specific Training Needs
Your EAP might check the box for "medical emergencies," but does your team actually know how to respond to an opioid overdose? With the unfortunate rise of synthetic opioids, this has become a very real workplace risk. A plan that doesn't account for this specific threat is simply incomplete.
Equipping your team with the right skills is vital, which is why understanding the importance of naloxone training is so critical for modern workplace safety.
EAP Mistake vs. Best Practice Solution
To help you spot these issues in your own plan, I've put together a quick comparison table. It highlights the common missteps and shows you the best-practice solution to get it right.
Common MistakeWhy It's a ProblemBest Practice SolutionUsing a Generic Template As-IsFails to address site-specific hazards like chemical storage or unique building layouts.Use the template as a guide, but conduct a full walkthrough and customize every section to your facility.Outdated Contact InformationWastes precious time during an emergency when trying to reach key personnel or first responders.Schedule a quarterly review of all contact lists and integrate updates into HR's offboarding process.Lack of Specific TrainingEmployees know a plan exists but don't have the practical skills (e.g., AED use, first aid) to execute it.Go beyond fire drills. Conduct hands-on training for likely scenarios identified in your hazard assessment."Set It and Forget It" MindsetThe plan becomes obsolete as the business changes, making it unreliable and non-compliant.Treat the EAP as a living document. Schedule an annual review and update it after any significant workplace change.
Avoiding these common mistakes is about shifting your mindset. Think beyond the binder on the shelf. Conduct a thorough hazard assessment, walk through every procedure, and most importantly, ask your team for feedback. A plan that is built, tested, and updated with real-world conditions in mind is a plan that will actually work when you need it most.
Your EAP Questions Answered
Even with a solid template and a clear path forward, questions always come up. It's totally natural. Getting your Emergency Action Plan right means digging into the details, and some of them can feel a bit confusing. Let's cut through the jargon and get you some straightforward answers.
I've gathered some of the most common questions I hear from business owners and safety managers just like you. Think of this as your quick-reference guide to firm up your understanding and get this done with confidence.
Is an EAP Required for Every Single Business?
This is probably the most common question I get, and the answer is: almost, but not quite. OSHA’s general rule applies to nearly every employer out there. However, there's one key exception based on your company's size.
If you have 10 or fewer employees, you aren't technically required to have a written EAP. But—and this is the critical part—you still have to communicate the plan's elements to your staff verbally. Honestly, it’s just a best practice to put it in writing anyway. It keeps everyone on the same page and ensures nothing gets lost in translation.
How Often Should We Review and Update Our Plan?
An EAP is a living document, not a "set it and forget it" file. Think of it like software; it needs regular updates to stay effective. You absolutely must review and update your plan:
- Annually: At a minimum, schedule a yearly review to catch any changes you might have missed.
- When the plan itself changes: Any time you make a significant change, you have to let your employees know.
- When your workplace changes: This could be anything from hiring new key people, changing your facility's layout, or bringing in new types of hazardous materials.
A good rule of thumb is to treat your EAP as part of your core operational strategy. If something changes in your business, just ask yourself: "How does this impact our emergency plan?"
What Is the Difference Between an EAP and a Fire Prevention Plan?
This is a frequent point of confusion, but the distinction is pretty simple once you see it. They are two separate plans with different goals, even though they often overlap.
An Emergency Action Plan (EAP) is all about what to do after an emergency has already started. Its main purpose is employee safety—guiding them through evacuation, sheltering-in-place, and making sure everyone is accounted for.
A Fire Prevention Plan (FPP), on the other hand, is proactive. It details how you’ll prevent fires from starting in the first place. It covers things like how to handle flammable materials and control potential ignition sources. While OSHA requires both under different circumstances, a solid EAP is what guides your team’s immediate actions during a crisis.
Where Should the EAP Document Be Stored?
Your EAP is useless if nobody can find it when the pressure is on. OSHA is very clear that the plan must be kept at the workplace and be available for employees to review. Accessibility is everything.
Here are a few best practices I always recommend for storage:
- Digital Access: Put the plan on a shared company drive or internal network that every single employee can get to easily.
- Physical Copies: Keep printed copies in accessible spots, like the break room, common areas, and inside managers' offices. Don't just lock it away in one person's filing cabinet.
- Off-Site Backup: It's also a smart move to have an off-site backup in case an emergency prevents you from even getting into your building.
How Detailed Should Rescue and Medical Duties Be?
If your plan calls for certain employees to perform rescue or medical duties, you need to be extremely specific. Vague instructions like "assist injured personnel" won't cut it. Your EAP must clearly outline their specific roles, responsibilities, and the training they’ve received.
This is where hands-on skills become non-negotiable. Your plan might say an employee will perform CPR, but that's only possible if they've been properly trained. Understanding the process of getting your CPR and AED certification is a vital step for anyone you designate as a first-aid provider. Your EAP should document exactly who these certified individuals are, ensuring you have a team that’s not just named on paper but is genuinely prepared to act.
At Ready Response, we believe a plan is only as strong as the people trained to execute it. From OSHA-compliant group training to supplying the AEDs and medical kits your plan requires, we provide the tools and hands-on education to turn your safety document into a life-saving reality. Visit us at https://readyresponsepa.com to equip your team with the confidence to act when seconds matter most.
SEO Title: Your OSHA Emergency Action Plan Template: A GuideMeta Description: Use our OSHA emergency action plan template to create a compliant EAP. Our guide covers requirements, customization, and common mistakes to avoid.